Risk in automation is the clear make or break point in producing quality equipment that meets expectations. These risks come in many forms and often the obvious or assumptions create openings for things to be missed. We have a simple process for evaluating the risk on every project. I’ll first share some obvious and maybe not so obvious risk points and then I’ll share how we work through them.
Risk points:
- Part feeding/orientation
- A new process
- A new product
- Inspections
Risk scaler:
- Highest level of Risk: No one has done it before.
- Moderate level of Risk: Someone has done it before, just not you.
- Lowest level of Risk: You and others have done it before.
De-Risking:
- Highest level of Risk: No one has done it before. Establish a thoughtful and deliberate development plan.
- Moderate level of Risk: Someone has done it before, just not you. Establish and execute a plan to copy what has been done by others.
- Lowest level of Risk: You and others have done it before. Copy it. (“Warning” copying is harder than it sounds)
While these steps are very simple the power is in the details and execution of the plans. We would welcome sharing our experiences around this rule.
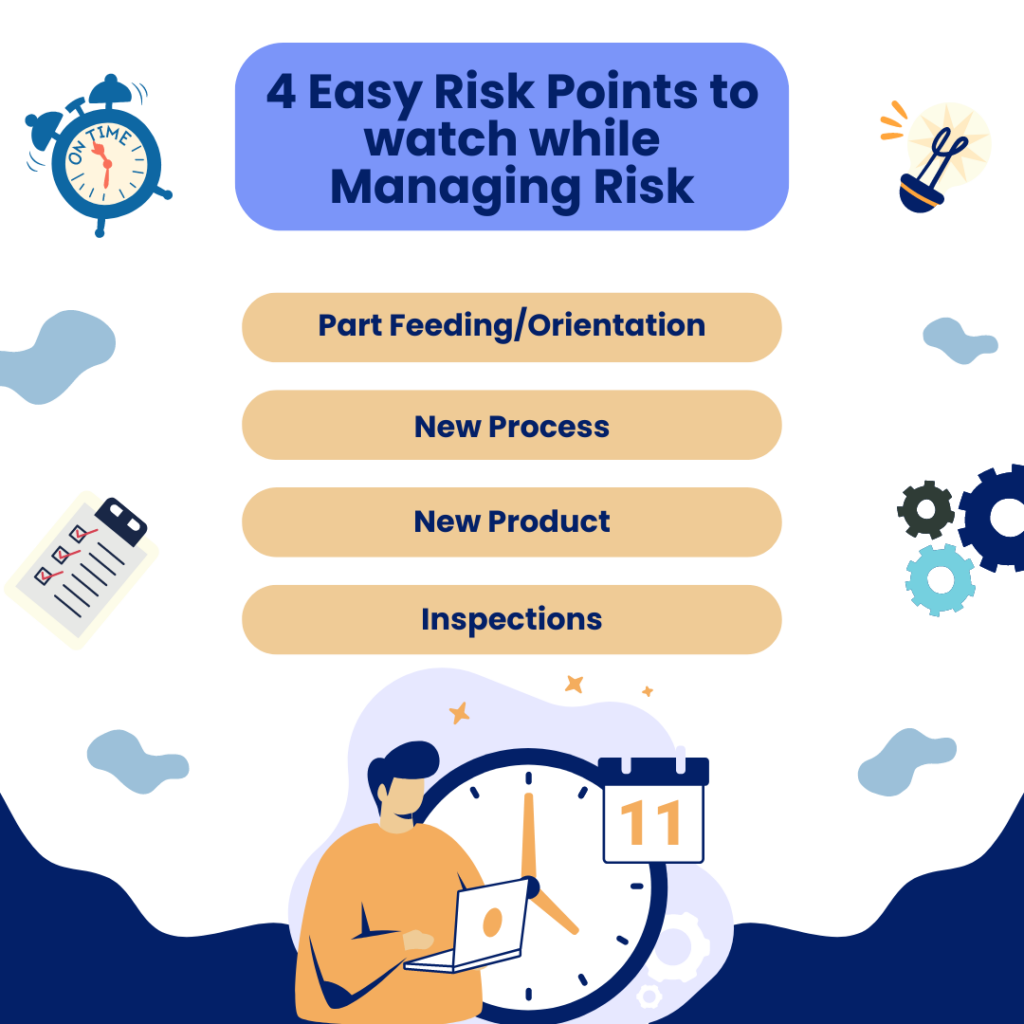